Revolutionizing Efficiency in Warehousing with Advanced Material Handling Systems
In today’s rapidly evolving marketplace, the efficiency of warehousing operations is pivotal for businesses striving to maintain a competitive edge. As companies increasingly turn to advanced technologies to streamline their logistics, the role of Material Handling Systems has become increasingly paramount. These systems not only enhance operational productivity but also play a critical role in optimizing inventory management and reducing labor costs. By implementing cutting-edge material handling solutions, organizations can significantly improve their workflow, minimize errors, and ensure faster turnaround times.
The integration of advanced Material Handling Systems is transforming traditional warehousing practices into agile and responsive operations capable of adapting to the dynamic demands of modern logistics. From automated storage and retrieval systems to sophisticated conveyor networks, the innovations in this field are enabling businesses to handle larger volumes of goods with greater accuracy and speed. As we delve deeper into the various aspects of these systems, it becomes evident that embracing these technologies is essential for companies looking to revolutionize their efficiency in warehousing and ultimately enhance customer satisfaction.
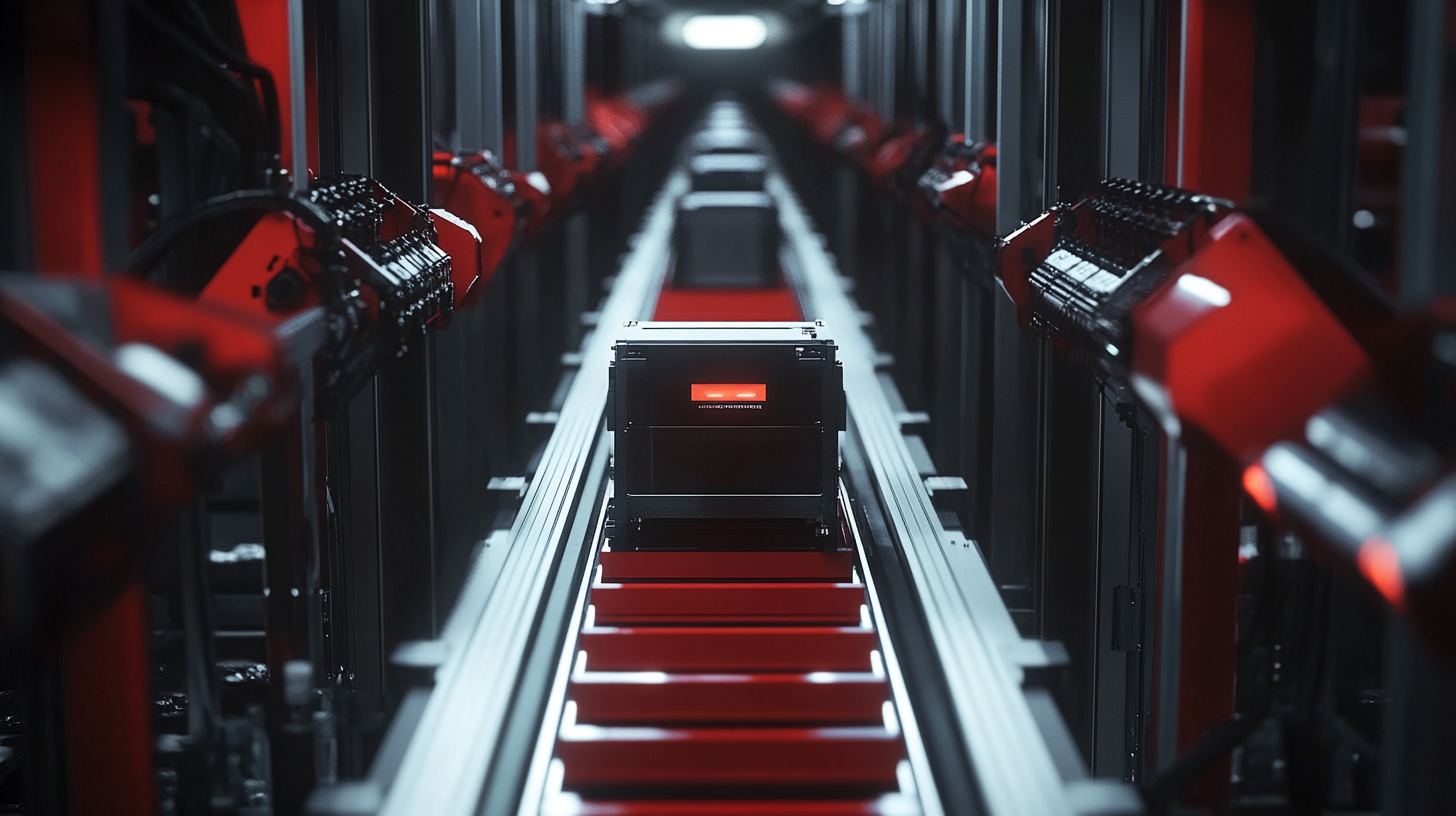
Understanding the Role of Automated Material Handling Systems in Modern Warehousing
Automated Material Handling Systems (AMHS) are transforming the landscape of modern warehousing by streamlining processes and enhancing operational efficiency. These advanced systems utilize robotics, conveyor belts, and automated guided vehicles (AGVs) to manage the movement of goods within facilities. By minimizing the need for manual labor, AMHS not only speeds up item retrieval and storage but also reduces the risk of human error, ensuring that products are handled with precision. The integration of AMHS in warehousing operations allows companies to adapt swiftly to changing market demands. With the ability to automate repetitive tasks such as picking, packing, and sorting, businesses can significantly increase their throughput. Furthermore, smart technologies within these systems enable real-time inventory tracking and data analysis, providing critical insights that help optimize stock levels and operational workflows. Moreover, the role of AMHS goes beyond mere efficiency; it contributes to enhancing workplace safety. Automated systems reduce worker exposure to potentially hazardous conditions, such as heavy lifting and traffic risks in busy warehouse environments. By leveraging advanced technologies, companies not only improve their bottom line but also create a safer, more productive environment for their workforce. With the ongoing advancements in automation, the future of warehousing promises even greater efficiency and safety through intelligent material handling solutions.
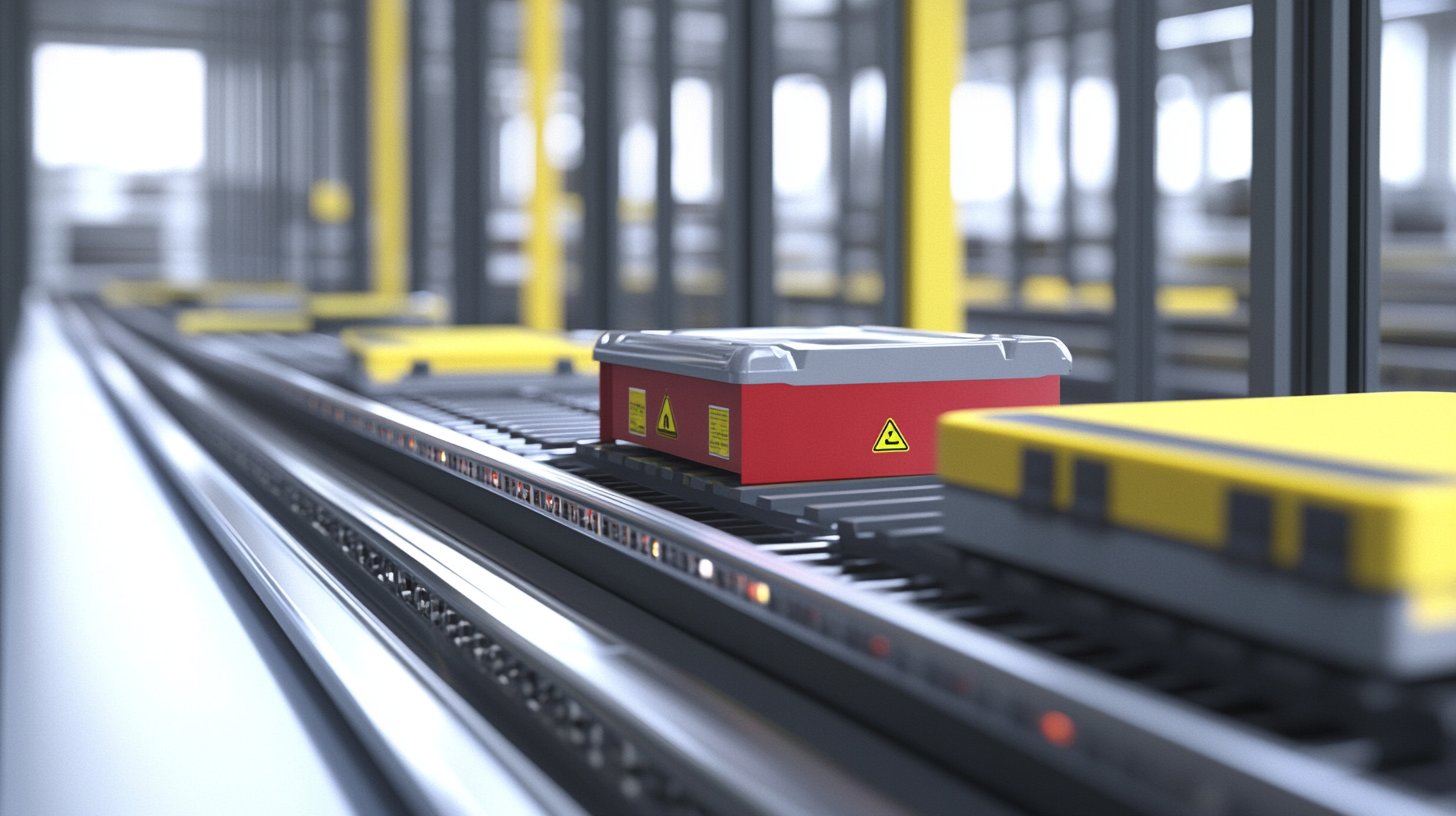
Key Metrics: How Advanced Systems Enhance Warehouse Productivity by Up to 30%
In today's rapidly evolving logistics landscape, advanced material handling systems are transforming the efficiency of warehouses. Implementing these state-of-the-art solutions can lead to remarkable enhancements in warehouse productivity, with metrics indicating improvements of up to 30%. This significant increase can be attributed to two key factors: automation and real-time data analytics.
Automation technologies, such as automated guided vehicles (AGVs) and robotic picking systems, streamline operations by reducing the time spent on manual tasks. By allowing machines to handle repetitive processes, warehouse staff can focus on more strategic activities, leading to faster order fulfillment and decreased operational costs. Moreover, with automation minimizing human error, accuracy in inventory management is greatly improved, further boosting overall productivity.
In addition, integrating real-time data analytics into material handling systems empowers warehouse managers to make informed decisions. By continuously monitoring performance metrics, they can identify bottlenecks and implement proactive solutions. This data-driven approach ensures that resources are allocated efficiently, optimizing workflow and enhancing the speed of operations. As companies adopt these advanced systems, they are not only revolutionizing their efficiency but also positioning themselves competitively in a demanding market.

The Impact of Robotics on Labor Efficiency in Material Handling Processes
The impact of robotics on labor efficiency in material handling processes cannot be overstated. As industries strive for higher productivity and streamlined operations, advanced robotics has emerged as a game changer in warehouses. These automated systems not only perform tasks previously mired in human inefficiencies but also enhance the accuracy and speed of material movement. This allows companies to focus their human resources on more strategic tasks, creating a workforce that is both versatile and more effectively utilized.
The integration of robotics into warehousing processes facilitates a remarkable reduction in human error, which is often a significant bottleneck in material handling. Automated guided vehicles (AGVs) and robotic arms are able to navigate complex warehouse layouts, picking and transporting goods without the hesitations or miscalculations that can occur with manual labor. Consequently, the accuracy of order fulfillment skyrockets, leading to increased customer satisfaction and reduced overhead costs related to returns and corrections.
Moreover, the ability of robots to operate continuously without fatigue further enhances labor efficiency. These machines can handle repetitive tasks that would be taxing for human workers, allowing employees to allocate their time and effort towards more complex operations that require critical thinking or creativity. By effectively complementing the human workforce, robotics not only boosts productivity but also fosters a safer working environment by minimizing risks associated with heavy lifting and repetitive strain injuries. This symbiotic relationship between human skills and robotic capabilities is paving the way for a new era of efficiency in warehousing.
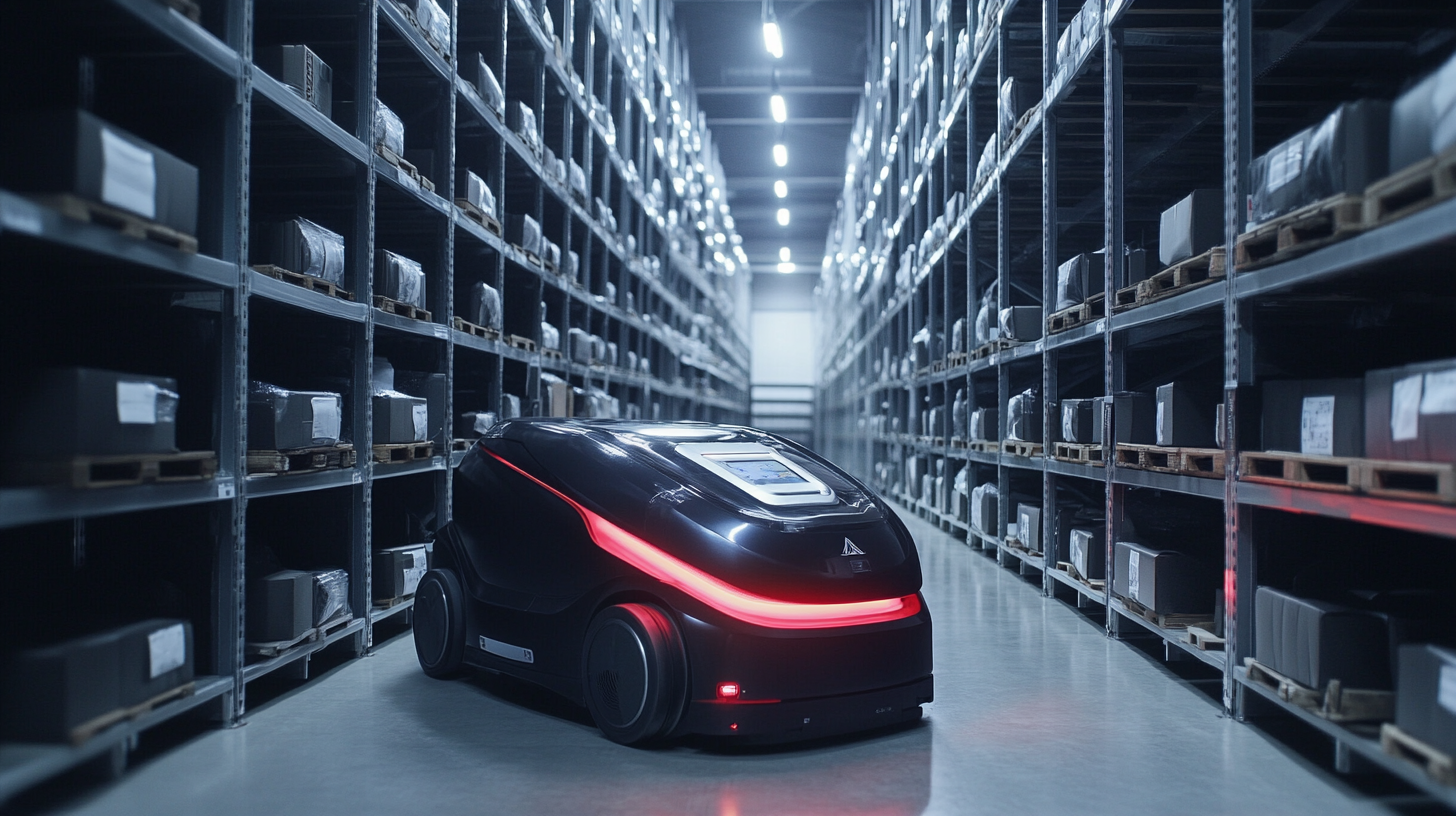
Cost-Benefit Analysis: Investing in Advanced Material Handling Technology for Long-term Savings
Investing in advanced material handling technology has become a pivotal decision for warehousing operations aiming to achieve long-term savings and enhanced efficiency. According to a report by the Material Handling Industry of America (MHIA), companies can boost productivity by as much as 30% through the implementation of automated systems that reduce manual labor and streamline processes. These systems, which include automated storage and retrieval systems (AS/RS) and conveyor systems, not only optimize space utilization but also minimize handling times, further contributing to operational savings.
Moreover, the return on investment (ROI) of advanced material handling systems is compelling. Research from the International Society of Automation (ISA) indicates that businesses typically see a payback period of 1.5 to 3 years, with some companies reporting operational cost reductions by up to 40%. These figures highlight the financial impact that strategic investments in technology can have. While the initial costs may appear significant, the long-term benefits—ranging from reduced labor costs to improved accuracy and lower error rates—far outweigh the upfront expenses.
Furthermore, a case study from the Warehousing Education and Research Council (WERC) revealed that facilities that adopted automated material handling solutions experienced a significant decrease in employee turnover rates, attributed to improved working conditions and reduced physical strain on staff. As safety and efficiency gain importance in modern warehousing, investing in advanced technology not only translates to fiscal responsibility but also fosters a more resilient and satisfied workforce.
Future Trends: The Evolution of AI and IoT in Shaping Warehousing Efficiency
The evolution of warehousing efficiency is being profoundly shaped by the integration of Artificial Intelligence (AI) and the Internet of Things (IoT). As noted in recent industry reports, the rapid advancement of computer and communication technologies has enabled significant improvements across all logistics segments, including warehousing, transportation, and distribution. Warehousing operations are becoming increasingly optimized through AI-powered robotics and automated sorting systems, leading to enhanced productivity and accuracy in inventory management.
Moreover, the concept of the smart supply chain is gaining traction. In today’s digital era, companies are leveraging data analytics and IoT sensors to gain real-time insights into their inventory, thus streamlining processes and reducing operational costs. A 2024 supply chain technology trend report highlighted that organizations that adopt these innovative technologies see up to a 30% increase in efficiency. Functions such as real-time tracking and automated replenishment are transforming traditional approaches, allowing warehouses to adapt to fluctuating demands and improve service quality.
Additionally, advancements in robotics and smart shelving systems play a crucial role in maximizing warehouse space utilization. As evidenced by a recent transformation initiative within the logistics sector, the combination of smart shuttle vehicles and high-density racking systems has led to a dramatic increase in storage capabilities, allowing businesses to accommodate greater volumes without requiring additional space. The ongoing integration of AI and IoT in warehousing does not merely enhance efficiency but also positions organizations to remain competitive in an evolving global economy.