Exploring the Future of Material Lifting Equipment Technology Trends and Their Global Impact in 2025
As we look ahead to 2025, the material lifting equipment industry is poised for significant advancements driven by innovation and evolving market demands. According to a report by Research and Markets, the global material handling equipment market is expected to reach $235 billion by 2025, highlighting the growing reliance on technology in industrial operations. With the rise of automation, smart technologies, and eco-friendly solutions, businesses must adapt to these trends to enhance efficiency and safety in material handling. This blog will explore the unique characteristics and applications of different types of material lifting equipment, as well as practical guidance on how to select the most appropriate solutions for various operational needs, ensuring that companies can navigate the shifting landscape of this critical industry effectively.
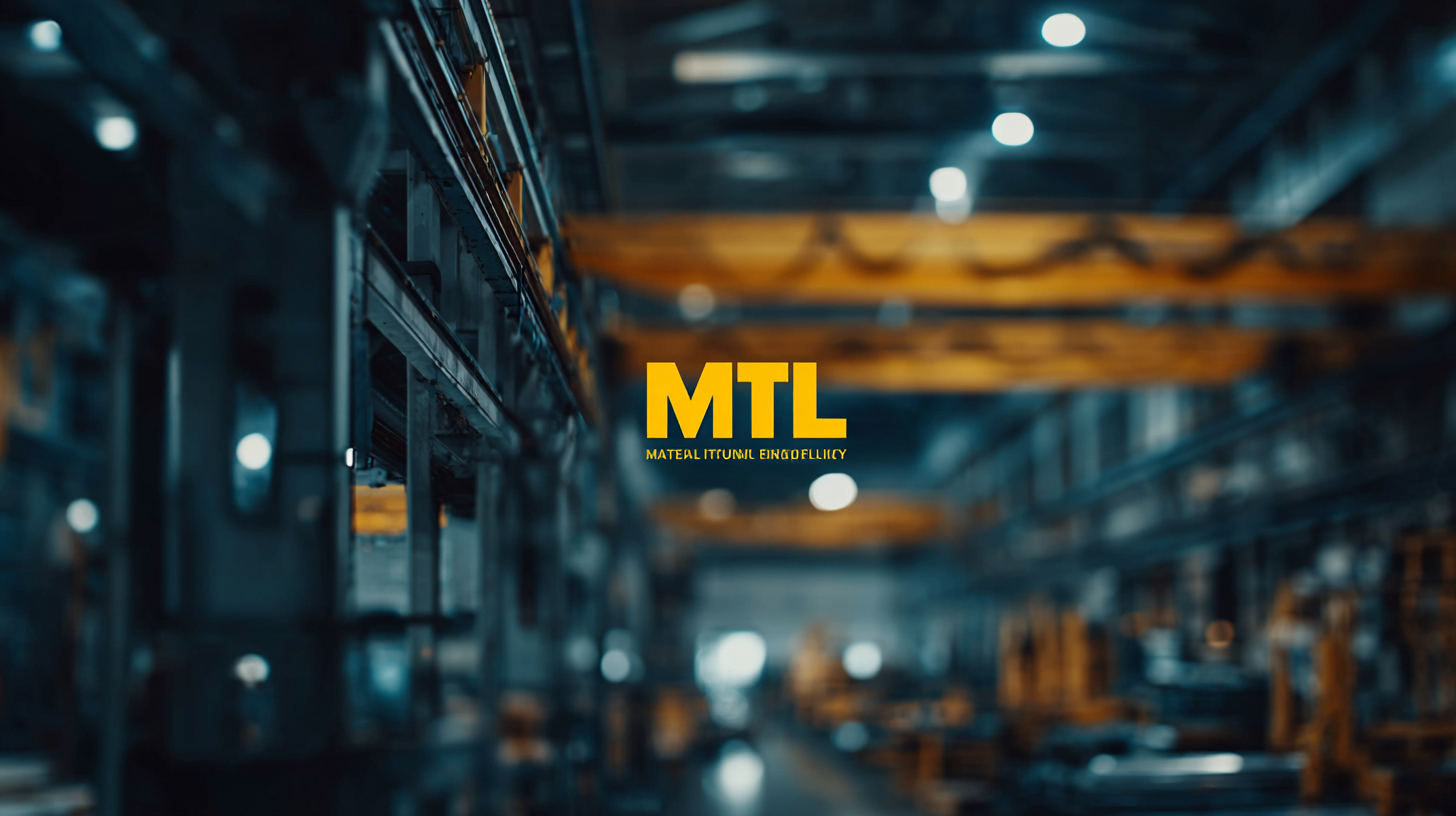
Types of Material Lifting Equipment: An Overview of Key Features
The landscape of material lifting equipment continues to evolve rapidly, driven by technological advancements and the increasing demand for efficiency across various industries. In 2025, we can expect several types of lifting equipment to become more prevalent, each featuring unique attributes designed to enhance their performance. Forklifts, for example, will likely see enhanced load capacity and improved maneuverability, making them indispensable in warehousing and material handling.
Another crucial type of lifting equipment is the telehandler, known for its versatility and ability to perform multiple tasks. With advanced telematics and safety features, telehandlers in 2025 will provide operators with real-time data, optimizing load management and reducing the risk of accidents. Additionally, electric-powered lifting equipment is set to gain prominence, thanks to its lower carbon footprint and operational costs. These innovations will not only improve job site safety but also address the global need for sustainable practices in material handling.
Understanding the Unique Applications of Cranes in Different Industries
In the realm of construction and manufacturing, cranes have become indispensable, adapting to a variety of unique applications across diverse industries. The tower crane, in particular, stands out for its ability to handle heavy lifting in urban settings, proving crucial in the construction of skyscrapers and large infrastructure projects. With a market poised for steady growth due to increasing urbanization and development projects, the demand for tower cranes is expected to rise significantly in the coming years.
Moreover, as industries continue to innovate, specialized cranes are being designed to meet specific operational needs. For instance, overhead cranes are gaining traction in manufacturing environments such as semiconductor cleanrooms, where precision and reliability are paramount. The versatility of cranes is further highlighted in the boom truck segment, which is experiencing a robust growth rate, driven by their application in both construction and maintenance tasks across various sectors. The ongoing advancements in crane technology ensure that they will remain a vital component in the transformation of industries globally.
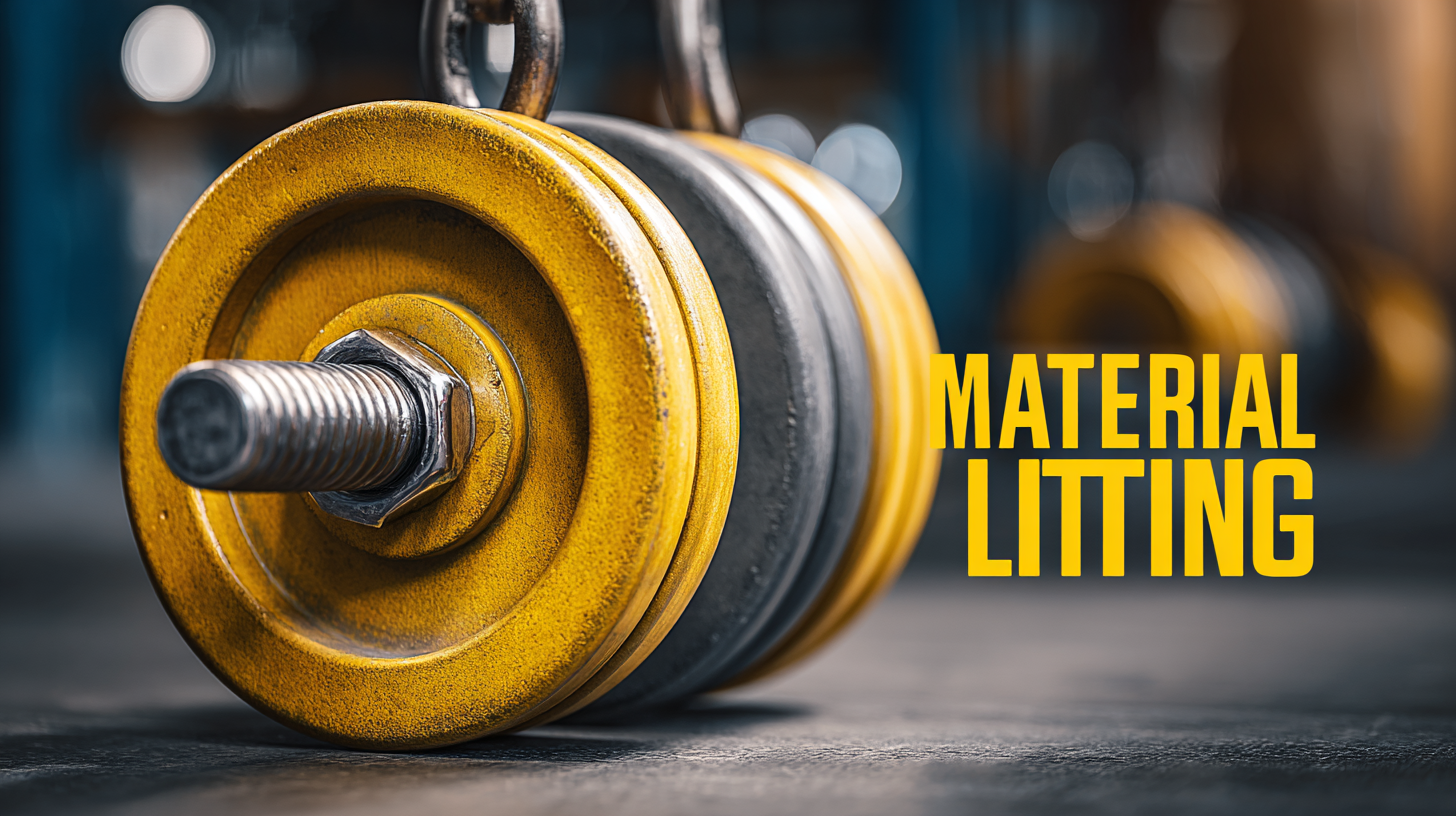
Forklifts vs. Hoists: Choosing the Right Equipment for Your Lifting Needs
When choosing between forklifts and hoists for your lifting needs, it's essential to consider the specific requirements of your operation. Forklifts are designed primarily for moving and stacking loads over short distances, making them ideal for warehouses and loading docks. In contrast, hoists excel in vertical lifting operations, suitable for construction sites and situations where space is limited. According to recent industry reports, the global market for material handling equipment is projected to grow steadily, with demand for both forklifts and hoists increasing due to advancements in technology and shifting economic trends.
**Tip 1**: Assess your operational space before making a choice. For confined or tall locations, a hoist may provide a more efficient solution. On the other hand, if you're managing large pallets or materials in an expansive area, a forklift would be more advantageous.
Moreover, safety is paramount in any lifting operation. Recent stats show a concerning trend with accidents involving elevating work platforms, highlighting the need for rigorous safety training and protocols.
**Tip 2**: Ensure all operators are trained on the specific machinery they will be using to adhere to safety standards and minimize risks. Regular maintenance of equipment is also crucial to ensure reliable performance and safety compliance.
Exploring the Future of Material Lifting Equipment Technology Trends and Their Global Impact in 2025
Equipment Type | Load Capacity (tons) | Max Lift Height (meters) | Power Source | Adoption Rate (%) |
---|---|---|---|---|
Forklifts | 5 | 4.5 | Electric / Diesel | 45 |
Hoists | 2 | 20 | Electric / Manual | 35 |
Cranes | 10 | 30 | Electric / Diesel | 25 |
Mobile Elevating Work Platforms | 0.5 | 12 | Electric | 40 |
Chain Blocks | 3 | 10 | Manual | 50 |
The Role of Automation in Advancing Material Lifting Technology
As we venture into 2025, the landscape of material lifting equipment is set to be transformed by the integration of automation. Automated systems enhance not only efficiency but also safety in various industries. With AI and machine learning at their core, these advanced technologies enable lifting equipment to make real-time decisions, optimizing load management and reducing the risk of human error. This evolution is crucial in sectors where precision is paramount, such as construction and manufacturing.
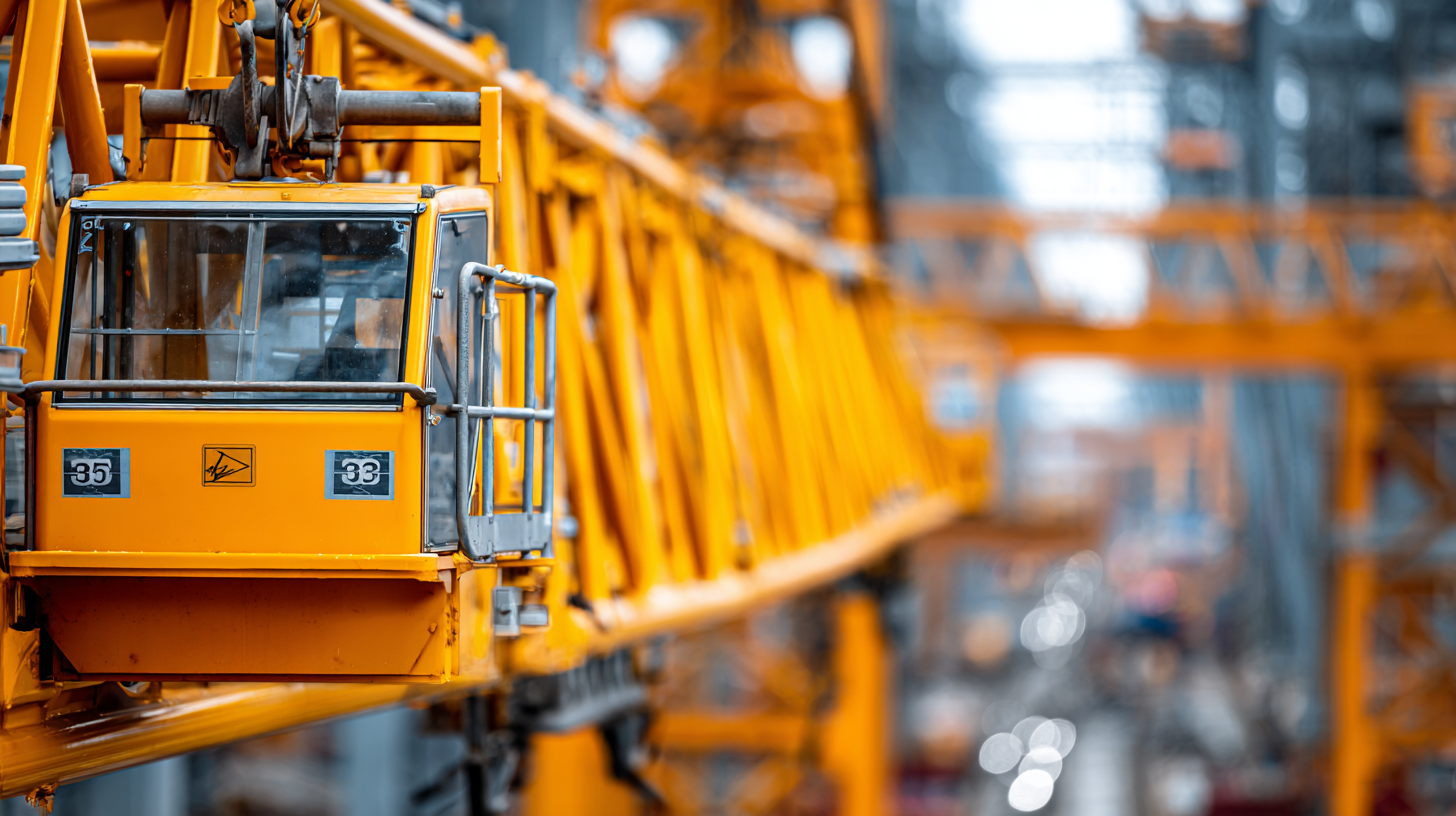
Tips for adopting automated material lifting solutions include starting with a thorough assessment of your current operations to identify areas where automation can have the most significant impact. Additionally, investing in training for your workforce is essential; even with automation, human oversight and intervention will still be critical for safety and optimal performance.
Furthermore, companies should prioritize the integration of IoT technology, which allows for seamless communication between lifting equipment and management systems. This interconnectedness not only streamlines logistics but also facilitates predictive maintenance, ensuring that equipment is always in optimal working condition. As industries gear up for this technological shift, embracing automation is not just an upgrade—it’s a necessity for staying competitive in a rapidly evolving market.
Sustainability in Material Lifting: Eco-Friendly Innovations and Trends
As we look toward 2025, the push for sustainability in material lifting equipment is reshaping the industry landscape. Eco-friendly innovations are becoming increasingly critical as companies strive to reduce their carbon footprints. From electric forklifts to solar-powered hoists, manufacturers are investing in technologies that not only enhance efficiency but also minimize environmental impact. These advancements are crucial for meeting the growing demand for greener logistics practices across various sectors.
In addition to alternative energy sources, new materials are being integrated into the design of lifting equipment. Lightweight composites and recyclables are gaining traction, providing durability while reducing weight and energy consumption during operation. These eco-conscious materials combine functionality with a commitment to sustainability, aligning with global initiatives aimed at promoting responsible manufacturing. As businesses adopt these innovative practices, they not only comply with regulations but also enhance corporate responsibility, contributing to a more sustainable future in the material handling industry.